DELTASHEILD HYBRID 500
Your Title Goes Here
Your content goes here. Edit or remove this text inline or in the module Content settings. You can also style every aspect of this content in the module Design settings and even apply custom CSS to this text in the module Advanced settings.
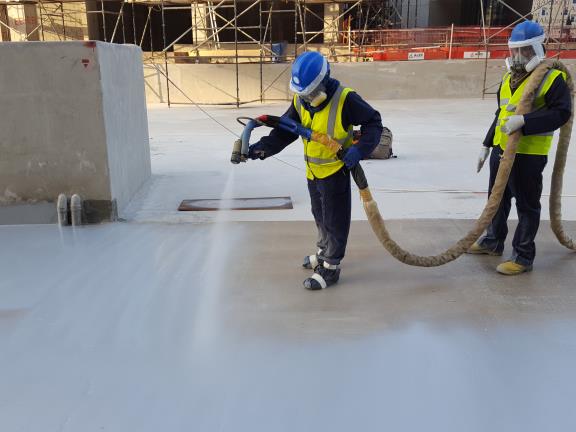
bout Us
DELTAShield Hybrid 500
Two component spray applied, semless general-purpose protective lining
Description
DELTAShield Hybrid 500 is a spray applied, instant curing flexible membrane formulated from hybrid Polyurea technology, that can be built to any thickness in one application.
This dynamic product provides a very flexible, seamless, hard-wearing substrate waterproofing and substrate protection solution for a wide range of substrates.
Its rapid spray application and instant curing characteristics enable shorter application times than traditional glue or weld in place and torch on membranes.
Waterproofing integrity around difficult shapes and multiple substrate types is easily achieved with DELTAShield Hybrid 500 removing these application risks.
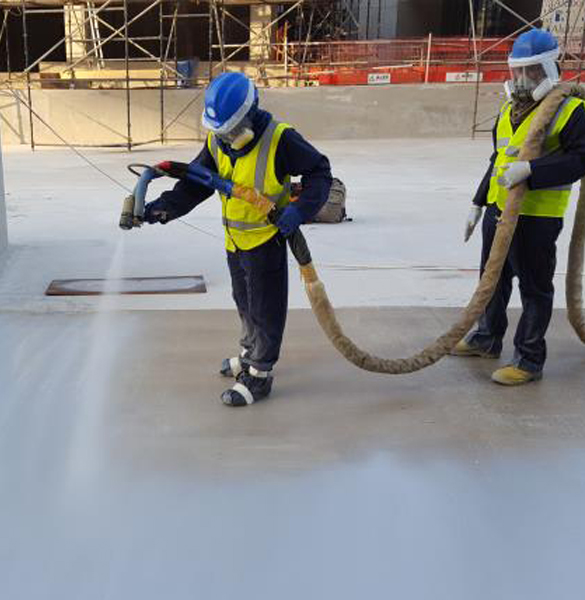
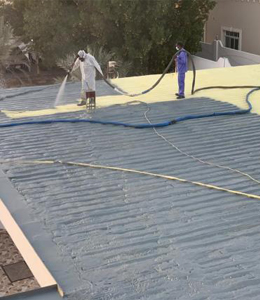
DELTAShield Hybrid 500
Two component spray applied, semless general-purpose protective lining
Description
DELTAShield Hybrid 500 is a spray applied, instant curing flexible membrane formulated from hybrid Polyurea technology, that can be built to any thickness in one application.
This dynamic product provides a very flexible, seamless, hard-wearing substrate waterproofing and substrate protection solution for a wide range of substrates./
Its rapid spray application and instant curing characteristics enable shorter application times than traditional glue or weld in place and torch on membranes.
Waterproofing integrity around difficult shapes and multiple substrate types is easily achieved with DELTAShield Hybrid 500 removing these application risks.
Features
- High Elongation property
- Excellent cost to benefits ratio
- Extremely fast application time
- Tack free in seconds – walk on in minutes
- Rapid return to service saves time and money
- Seamless Waterproofing. No welding of joints – totally seamless.
- Conforms exactly to substrate shapes eliminating potential stress points when covering with final floor slabs or other toppings such as pavers.
- Excellent adhesion to nearly all substrates – concrete, steel, aluminum, wood, foam etc.
- Can transgress multiple substrate types in one application
- Good tensile and structural strength
- No need to use protector boards when back filling
- 100% solids, VOC-free, Solvent free
- Good abrasion resistance
- Good impact resistance
- Excellent thermal stability
Typical Uses
- Large scale Waterproofing for Commercial, Industrial & manufacturing facilities
- Waterproofing of high impact areas. – Plant rooms, trafficable roof decks
- Waterproofing for areas exposed to high wind abrasion
- Waterproofing of water features, pools and ponds
- Under concrete screed Waterproofing of large-scale podium decks
- Bridge, street and tunnel construction Waterproofing
- Waterproofing and containment applications where high humidity and high levels of residual moisture are not factors to be considered during application
- Anti-root sub terrain Waterproofing.
Property | Data |
---|---|
Mixing ratio of Comp. A to Comp. B | 1:1 by volume |
Material consumption [kg/m2/1mm] | Approx. 1 |
Dry film thickness range [mm] For project specific DFT recommendations consult with manufacturer. |
Steel Minimum: 1 Maximum: indefinite Concrete Minimum: 2 Maximum: indefinite |
Recommended thickness [mm] | Minimum: 2 on concrete Max: unlimited. |
Tack Free-Time at 20°C [sec.] | 10 – 20 |
Over coat window [h] | 0 – 12 hours (without prep and priming) |
Curing/loading after [h] | Foot traffic: 1 Mechanical: 2 Chemical: 12 – 24 |
Temperature range for application (ambient) [°C] | -10 to +50 |
Temperature range for application (substrate) [°C] | -10 to +50 |
Material Temperature (Preconditioning) [°C] | 25 – 30 |
Material Temperature (Spraying) [°C] | 65 – 75 |
Maximal relative air humidity for application [%] | 80 – 85 |
Pay attention to the dew point limit | Substrate should be 3°C greater than DP (dew point) |
Property | Test Standard | Comp. A Data | Comp. B Data |
---|---|---|---|
Chemical Base | – | MDI – Prepolymer | Polyether amine and Polyol – Mixture |
VOC-content | DIN EN ISO 11890-1 / ASTM D-1259 | 0% | 0% |
Solids content | DIN EN 827 / ASTM D-2697 | 100% | 100% |
Viscosity [mPas] @ 23°C (cone and plate, S3, 100rpm) | DIN EN ISO 329/A3 / ASTM D-4878 | 1,500 – 2,000 | 2,000 – 2,000 |
Density [g/ml] | DIN EN ISO 2811-1 / ASTM D-1217 | 1.09 – 1.13 | 1.05 – 1.20 |
Density [g/cm3] | EN ISO 1183 / ASTM D-792 | 1.00 ± 0.02 | 1.00 ± 0.02 |
Tensile strength [MPa] | ISO 37-2005 / ASTM D-412 | ≥ 14-16 | ≥ 14-16 |
Elongation at break [%] | ISO 37-2005 / ASTM D-638 | 500 – 550 | 500 – 550 |
Hardness [Shore D] | ISO 868-2003 / ASTM D-2240 | 40 ± 5 | 40 ± 5 |
Tear strength [kN/mm] | ISO 34-1 method A | 40 | 40 |
Taber Abrasion [mg] | ASTM D-4060 | < 10 (Wheel CS17 / 1,000g / 1,000 Cycles) | < 110 (Wheel H18 / 1,000g / 1,000 Cycles) |
Pull off strength [N/mm2] | DIN EN ISO 4624 / ASTM D-4541 | Concrete: ≥ 1.5 Steel: ≥ 4 |
Concrete: ≥ 1.5 Steel: ≥ 4 |
Storage conditions [°C] | DIN EN 12701 | 10 – 30 (Avoid product freezing) | 10 – 30 (Avoid product freezing) |
Shelf life | – | Approximately 12 months unopened and stored correctly | Approximately 12 months unopened and stored correctly |
- All applicators of DELTAShield Hybrid 500 should be trained and approved by the manufacturer.
- Spray applicators should wear appropriate PPE including approved breathing equipment, eye wear, Nylex or similar light weight spray suit and appropriate covered footwear.
- Avoid breathing in vapors during spraying or when handling chemicals.
- Avoid eye and skin contact.
- Store chemical drums in a cool dry environment. Avoid storing chemicals for long periods in direct sunlight.
- Do not store chemicals next to food stuffs.
- Ensure chemical drums are kept tightly sealed and avoid ingress of air and moisture.
DELTAShield Hybrid 500 is supplied in 40 or 425 kg sets.