DELTAShield F 500
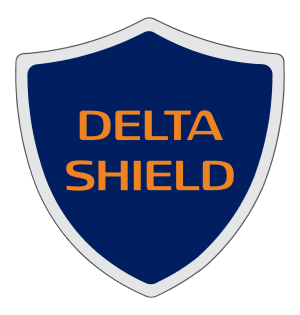
DELTAShield F 500
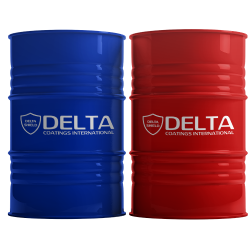
Description
DELTAShield F 500 is a high performance, rapid curing, self levelling, high gloss flooring product based on the latest polyaspartic / polyurea technologies.
This dynamic product provides excellent colour and gloss retention and is resistant to most fuels, oils, solvents, and cleaners. DELTAShield F 500 can be applied using an airless spray gun or rollers.
With a tack free time of 60 minutes re-use times are incredibly short saving customers’ costly down time.
DELTAShield F 500 can be pigmented and can incorporate colored flakes or aggregates. When applied clear DELTAShield F 500 provides a superior anti-yellowing top-coat sealer.
Features
- Extremely fast cure and re-use times
- Excellent colour and gloss retention
- Excellent self levelling characteristics.
- Cures to a very clear finish when not pigmented
- Excellent abrasion resistance
- Self-priming
- Excellent adhesion to concrete substrates
- Excellent chemical resistance
- Resistant to most chemicals, solvents, acids and caustics
- Can be used for indoor and outdoor applications
- Stable over a wide temperature range
- Displays good flexibility and impact resistance compared to standard epoxies.
- UV Stable in clear or pigmented form.
Typical Uses
- As a seamless rapid application, 1 product, 1 application, commercial and Industrial flooring system
- Aircraft hangers
- Warehouse flooring
- Restaurants and kitchens
- Retail shops and shopping malls
- Hospital flooring
- Car park decks
- As a self-leveling, high gloss sealing coat for flake and quartz decorative flooring
- As a non-yellowing sealer for stone and timber
- As a refurbishment coat over old epoxy or polyurethane floors
View more information
Processing Properties
Property | Data |
---|---|
Mixing ratio of Comp. A to Comp. B | 1:1 by volume |
Material consumption – approximate L / m2 | 0.25ml @ 250 μm (Substrate dependent) |
Recommended thickness [μm] | 125 – 1000 |
Recommended layer thickness [μm] | Up to 500 |
Pot life at 20°C [min.] | 45 – 50 |
Tack free time @ 20°C, 57% humidity [min.] | 45 |
Pedestrian traffic after [h] | Light use: 4 Heavy use: 8 – 10 |
Full Cure (Normal loading) [h] | 12 |
Temperature range for application (ambience) [°C] | +5 – +50 |
Temperature range for application (substrate) [°C] | +5 – +50 |
Over coat window (h) | 8 |
Physical Properties
Property | Test Standard | Comp. A Data | Comp. B Data | Mix Data |
---|---|---|---|---|
Chemical Base | – | Polyaspartic / Polyurea technology | Polyaspartic / Polyurea technology | – |
Solids content [%] | DIN EN ISO 3251 | 97 | 97 | – |
Viscosity [mPa*s] @ 25°C | DIN EN ISO 3219 / A3 | 100 | 1940 | Mix: approx. 570 |
Density [g/cm³] @ 20°C | DIN EN ISO 2811-1 / ASTM D-1217 | 1.18 – 1.22 | 1.07 – 1.11 | 1.15 |
Density [g/cm³] | EN ISO 1183 / ASTM D-792 | 1.23 ± 0.02 | 1.23 ± 0.02 | – |
Tensile strength [Mpa] | ISO 37-2005 / ASTM D-638 | ≥ 16 | ≥ 16 | – |
Property | Test Standard | Comp. A Data | Comp. B Data | Mix Data |
---|---|---|---|---|
Chemical Base | – | Polyaspartic / Polyurea technology | Polyaspartic / Polyurea technology | – |
Solids content [%] | DIN EN ISO 3251 | 97 | 97 | – |
Viscosity [mPa*s] @ 25°C | DIN EN ISO 3219 / A3 | 100 | 1940 | Mix: approx. 570 |
Density [g/cm³] @ 20°C | DIN EN ISO 2811-1 / ASTM D-1217 | 1.18 – 1.22 | 1.07 – 1.11 | 1.15 |
Density [g/cm³] | EN ISO 1183 / ASTM D-792 | 1.23 ± 0.02 | 1.23 ± 0.02 | – |
Tensile strength [Mpa] | ISO 37-2005 / ASTM D-638 | ≥ 16 | ≥ 16 | – |
Elongation at tear [%] | ISO 37-2005 / ASTM D-638 | ≥ 178 | ≥ 178 | – |
Hardness [Shore D] | ISO 868-2003 / ASTM D-2240 | 75 | 75 | – |
Rebound resilience [%] | ISO 4662 / ASTM | ≥ 5 | ≥ 5 | – |
Taber Abrasion [mg] | ASTM D-4060 | < 30 (Wheel CS17 / 1.000g / 1000 cycles) | < 30 (Wheel CS17 / 1.000g / 1000 cycles) | – |
Colour fastness | DIN EN ISO 105-B06 | No chalking, no dis-coloration, no cracking and no blistering. | No chalking, no dis-coloration, no cracking and no blistering. | – |
Colour fastness | ASTM G154a / ISO 4892 | After approx. 500 hours: No chalking, no dis-coloration, no cracking and no blistering. |
After approx. 500 hours: No chalking, no dis-coloration, no cracking and no blistering. |
– |
Storage conditions [°C] | DIN EN 12701 / ASTM | 10 – 30 (in closed original drums, stored at dry and well-ventilated place. Avoid freezing) | 10 – 30 (in closed original drums, stored at dry and well-ventilated place. Avoid freezing) | – |
Shelf life | – | Approximately 12 months | Approximately 12 months | – |
Packaging
DELTAShield F 500 is supplied in 5 or 20 kg packaging for each component individually.
All guidelines, recommendations, statements, and technical data contained herein are based on information and tests we believe to be reliable and correct, but accuracy and completeness of said tests are not guaranteed and are not to be construed as a warranty, either expressed or implied. It is the user`s responsibility to satisfy himself, by his own investigations and testing, the suitability of the product for his own intended use, application and job situation and user assumes all risk and liability resulting from his use of the product. Due to the large number of variables that can affect the product and the application process that are out of the control of DELTA Coatings International LLC no warranty of any kind, express or implied is given. The liability of DELTA Coatings International LLC for any claims is limited to the purchase value of the material.
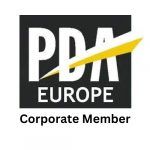
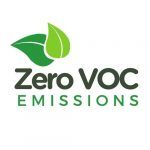
