DELTAShield HP 400
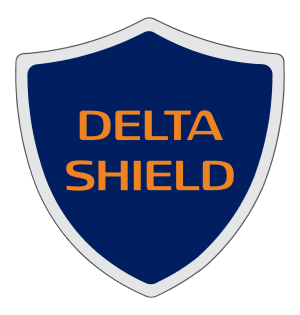
DELTAShield HP 400
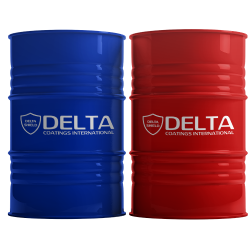
VIEW OUR PROJECT REFERENCES
Description
DELTAShield HP 400 is an instant curing, spray applied, seamless, and flexible protective membrane. This best-in-class product sits at the top of DELTA`s high performance coatings range and is suitable for use in a wide range of demanding applications requiring abrasion, impact and chemical resistance.
Our dynamic product is an excellent primary and secondary containment membrane providing seamless, instant curing, flexible containment solutions that require a higher performance level than standard waterproofing membranes. DELTAShield HP 400 is an ideal lining for abrasive liquid containment, industrial, chemical and impact applications.
Features
- Can be applied even under extreme climatic conditions. Hot, cold and humid conditions
- Very good abrasion, impact and chemical resistance for most applications
- Resistant to most standard chemicals, acids, oils, and bleaches
- Very good elongation at break
- Very good tensile strength
- Suitable for exposed applications
- Seamless application and seamless finish. No welded joints or glued seams
- Excellent adhesion to concrete, steel, aluminum, plastics, fibers, wood, foam etc.
- Can be applied across multiple substrates in the same application process
- Remains flexible under a wide range of climatic conditions
- Rapid application to any thickness and very fast cure results in faster turnaround times
- Can build to any thickness in one application
- Does NOT require multiple coats
- 100 % solids, VOC-free, contains zero solvents
Typical Uses
- Protection of concrete substrates in water and wastewater treatment plants.
- Steel and concrete tank linings subject to corrosion, abrasion and chemical attack.
- Waterproofing of areas subject to impact, abrasion, traffic loads, UV exposure.
- Protection of substrates against abrasion and impact in materials handling applications. – Mining, concrete manufacture, concrete batching plants, sand and gravel quarries.
- Sacrificial wear plates and linings in the mining and transport industries.
- Secondary containment linings in the power, petro chemical, oil and gas industries.
- Applications where substrates are being subjected to abrasion, impact and corrosion in industrial applications.
View more information
Processing Properties
Property | Data |
---|---|
Mixing ratio of Comp. A to Comp. B | 1 : 1 by volume |
Dry film thickness range [mm] | Steel Minimum: 1 Steel Maximum: indefinite Concrete Minimum: 2 Concrete Maximum: indefinite For project specific DFT recommendations consult with manufacturer. |
Recommended thickness [mm] | Minimum: 1 Maximum: unlimited |
Tack Free-Time at 20°C [sec.] | 10 – 20 |
Over coat cycle [h] | 0 – 12 (without any pre-treatment) |
Curing/loading after [h] | Walkable: 1 Mechanical: 2 Chemical: 12 – 24 |
Temperature range for application (ambient) [°C] | -10 – +50°C |
Temperature range for application (substrate) [°C] | -10 – +50°C |
Material Temperature (Preconditioning) [°C] | 25 – 30°C |
Material Temperature (Spraying) [°C] | 65 – 75°C |
Maximal relative air humidity for application [%] | 98% |
Pay attention to the dew point limit | Substrate should be 3°C greater than DP (dew point) |
Physical Properties
Property | Test Standard | Comp. A Data | Comp. B Data |
---|---|---|---|
VOC-content | DIN EN ISO 11890-1 / ASTM D-1259 | 0% | 0% |
Solids content | DIN EN 827 / ASTM D-2697 | 100% | 100% |
Viscosity [mPa*s] @ 25°C | DIN EN ISO 2884-2 / ASTM D-4878 | 600 – 1,000 | 500 – 900 |
Density [g/cm³] @ 20°C | DIN EN ISO 2811-1 / ASTM D-1217 | 1.09 ± 1.13 | 1.00 ± 1.04 |
Density [g/cm³] | EN ISO 1183 / ASTM D-792 | 1.01 ± 1.05 | 1.01 ± 1.05 |
Tensile strength [MPa] | ISO 37-2005 / ASTM D-638 | ≥ 20 | ≥ 20 |
Modul [MPa] | ISO 37-2005 / ASTM D-638 | 100% Elongation: ≥ 10 300% Elongation: 20 |
100% Elongation: ≥ 10 300% Elongation: 20 |
Elongation at break [%] | ISO 37-2005 / ASTM D-638 | ≥ 400 – 450 | ≥ 400 – 450 |
Hardness [Shore D] | ISO 868-2003 / ASTM D-2240 | 45 ± 5 | 45 ± 5 |
Property | Test Standard | Data |
---|---|---|
Rebound resilience [%] | ISO 4662 / ASTM | ≥ 32 |
Tear growth resistance[N/mm] | ISO 34-1 method A | ≥ 45 |
Volume abrasion [mm³] | DIN ISO 4649 | ≤ 130 |
Taber Abrasion [mg] | ASTM D-4060 | < 6 (Wheel CS17 / 1.000g / 1000 Cycles) < 125 (Wheel H18 / 1.000g / 1000 Cycles) |
Pull off strength [N/mm²] | DIN EN ISO 4624 / ASTM D-4541 | Concrete: ≥ 1.5 Steel: ≥ 6 |
Max. Process temp. [°C] | ISO 11346 / ASTM D-2485 | Wet: 80 Dry: 130 Peak temperature dry: 160 |
Water vapor transmission rate [g/m² *d] | ISO 15106-3 | 6.1 (at 23°C a. 85% relative humidity) 17.5 (at 38°C a. 90% relative humidity) |
Permeation coefficient [g*mm/m²*d] | ISO 15106-3 | 17.3 (at 23°C a. 85% relative humidity) 51.0 (at 38°C a. 90% relative humidity) |
Methane transmission rate [cm³/m²*d*bar] | ISO 15105-1 | 91.5 (at 23°C a. 0% relative humidity) |
Resistance to Root Penetration | EN 14416 | Passed |
Crack bridging abilities [mm] (thickness of the sample 2-3 mm) | DIN EN 1062-7 Procedure C.2 | +23°C: > 15.5 -10°C: > 6.8 -20°C: > 6.4 |
Fire protection classification | DIN 4102-Part 1 | B2 (normally inflammable) |
Coefficient of sliding friction | DIN 51131 | Dry (leather): 0.78 Wet (SBR-rubber): 0.04 |
Sound absorption | – | Approx. 5 dB / mm DFT |
Cathodic Disbondment depth [mm] | DIN EN 10290-2004 Class: A | 23°C (28 days): 2.3 ± 0.7 60°C (2 days): 1.7 ± 0.6 80°C (2 days): 3.4 ± 1.1 |
Property | Test Standard | Data |
---|---|---|
Impact Resistance [J/mm] | DIN EN 10290-2004 Class: A | 23°C: 9.0 -5°C: 7.0 |
Surface resistance [Ohm] | DIN IEC 60167 | ≥ 1.0*10^11 |
Volume resistance [Ohm] | DIN IEC 60093 | ≥ 1.0*10^11 |
Storage conditions [°C] | DIN EN 12701 | 10 – 30 (in closed original drums, stored at dry and well-ventilated place; beware of freezing) |
Shelf life | – | Approximately 18 months unopened and stored correctly |
Safety & Handling
- All applicators of DELTAShield HP 400 should be trained and approved by the manufacturer.
- Spray applicators should wear appropriate PPE including approved breathing equipment, eye wear, Nylex or similar light weight spray suit and appropriate covered footwear.
- Avoid breathing in vapors during spraying or when handling chemicals.
- Avoid eye and skin contact.
- Store chemical drums in a cool dry environment. Avoid storing chemicals for long periods in direct sunlight.
- Do not store chemicals next to food stuffs.
- Ensure chemical drums are kept tightly sealed and avoid ingress of air and moisture.
Packaging
DELTAShield HP 400 is supplied in 40 or 425 kg sets.
All guidelines, recommendations, statements, and technical data contained herein are based on information and tests we believe to be reliable and correct, but accuracy and completeness of said tests are not guaranteed and are not to be construed as a warranty, either expressed or implied. It is the user`s responsibility to satisfy himself, by his own investigations and testing, the suitability of the product for his own intended use, application and job situation and user assumes all risk and liability resulting from his use of the product. Due to the large number of variables that can affect the product and the application process that are out of the control of DELTA Coatings International LLC no warranty of any kind, express or implied is given. The liability of DELTA Coatings International LLC for any claims is limited to the purchase value of the material.
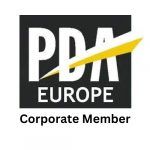
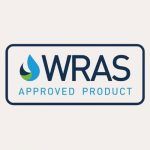

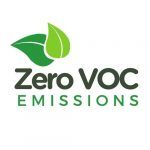